
Carbon capture: How waste incineration can become climate neutral
Processing residual waste provides valuable energy for heating, but it also produces emissions of greenhouse gases. Statkraft wants to reduce greenhouse gas emissions by capturing CO2 from its waste incineration plant in Trondheim and store it under the seabed in the North Sea.
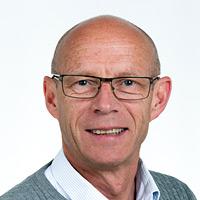
Bjørn Hølaas is director for carbon capture and storage (CCS) in Statkraft Varme and leads the work on realising the capture and storage of carbon emissions from waste incineration at the Heimdal district heating plant in Trondheim.
Several industrial processes, such as cement production and waste incineration, lead to emissions of greenhouse gases. For these processes, the capture and storage of carbon – often abbreviated to CCS – is the only option for cutting those emissions.
In Norway, there are more than 20 CCS projects of various sizes within industry, waste incineration and direct capture of CO2 from the air (DACCS) which can contribute considerably to reducing greenhouse gas emissions. Statkraft's waste incineration project at the district heating plant at Heimdal in Trondheim is one of them.
.
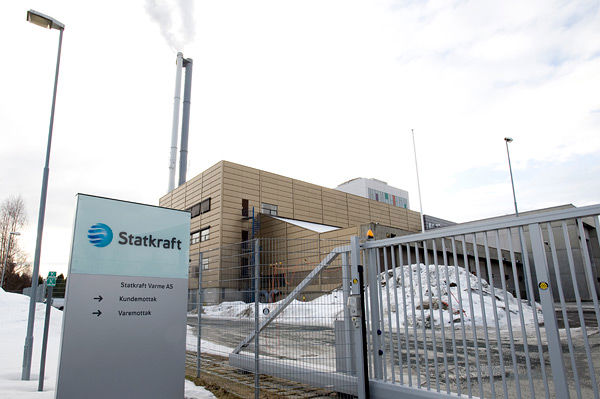
Effective use of resources
Treating waste in a modern incineration plant is the best and most climate-efficient way of final treatment, when the waste has no other utility value. A third of Trondheim's heating needs are met with district heating, which uses, among other sources, surplus energy from waste incineration. But waste incineration emits large volumes of CO2.
Heimdal district heating plant has total emissions of approximately 240,000 tonnes of CO2 per year from incineration of two types of waste; biogenic and fossil.
Emissions from the combustion of biogenic waste such as food waste, paper, wood and wood chips form part of a natural carbon cycle, and therefore do not contribute to greenhouse gas emissions. Emissions from the incineration of waste of fossil origin, such as plastics and synthetic textiles, have no such natural cycle and therefore contribute to CO2 emissions. At Heimdal, around a third of the CO2 emissions are fossil.
"Our heating plant accounts for 25 per cent of fossil CO2 emissions in Trondheim. The goal is to remove this through carbon capture and storage. In addition, the capture and storage of biogenic CO2 will contribute to further removal of CO2 from the atmosphere. Statkraft aims to have its entire district heating operations climate neutral by 2040," says the manager of the CCS project in Statkraft Varme, Bjørn Hølaas.
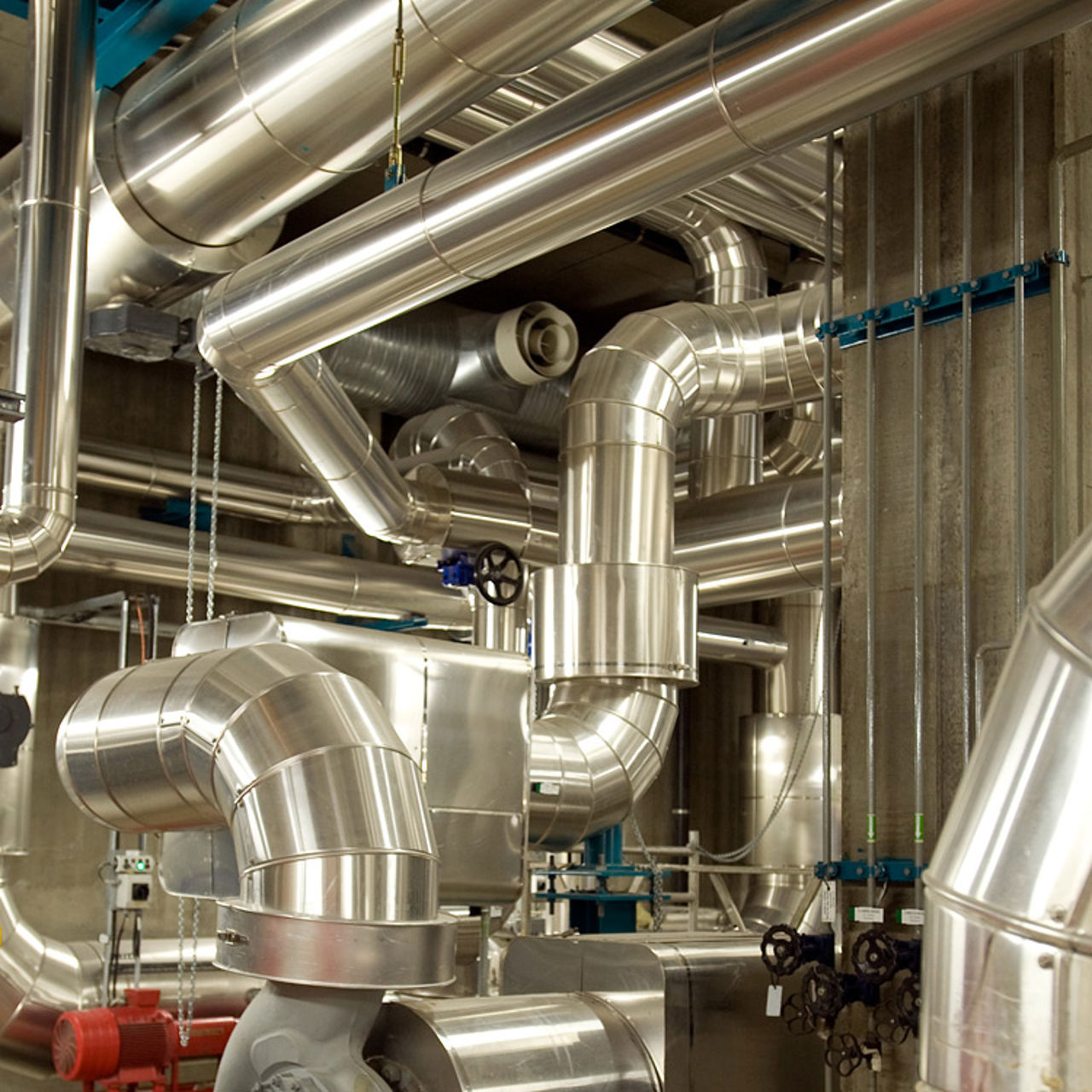
About Statkraft Varme
Statkraft Varme has utilised surplus energy to supply district heating and cooling since 1982 and has 130 employees in Norway and Sweden. The company annually produces over 1 TWh of district heating, equivalent to the normal annual heating needs of 140,000 flats.
More about Statkraft Varme (in Norwegian only)
Opens in new tab or windowHow is it done?
In a waste incineration plant, the greenhouse gases are mixed with the smoke that rises from the chimney. It is from this smoke that Statkraft Varme wants to filter and capture CO2.
"We plan to use the flue gas CO2 capture technology which is the most efficient and the most mature, namely amine technology," says Hølaas.
This technology uses chemicals that bind to the CO2 found in the flue gas, so that the smoke released from the smokestack is CO2-free. Once the carbon is captured, it can be cooled and pressurised before being shipped away in liquid form.
"This is the same technology that will be used at Norcem's cement factory in Brevik and at the waste incineration plant at Klemetsrud in Oslo," Hølaas points out.
Land-intensive capture plants and long-distance transport, but permanent storage
A carbon capture plant requires a lot of space, which is a challenge on an existing industrial site. The feasibility study carried out by Statkraft shows that there is no space for a carbon capture plant on the existing site of the Heimdal district heating plant, so adjoining areas need to be used.
"Preliminary calculations show a land requirement of around 7,000 square metres. However, we are conducting good dialogue with Trondheim municipality to find the necessary space to be able to realise the project," says Hølaas.
Once the greenhouse gas has been removed from the flue gas, it will be transported from the carbon capture plant in pressurised, liquid form in tanker trucks to an intermediate storage facility.
"The plan is to transport the gas 36 kilometres to an intermediate storage facility in Orkanger. We estimate that 21 trucks will be driven every day, each with 30 tonnes of CO2," says Hølaas.
From the port at Orkanger the carbon dioxide will be shipped to a receiving terminal at Øygarden outside Bergen. From there, it will be transported by pipeline into the North Sea and then pumped into porous rocks at a depth of over 2,500 metres. Denser rocks above the reservoir ensure that the gas does not leak out and end up in the atmosphere.
Once the CO2 is removed from the flue gas, it will be converted to liquid form and transported in tanker trucks from the carbon capture plant to an intermediate storage facility.
"The plan is to drive around 21 trucks a day, each with 30 tonnes of CO2, to the intermediate storage facility," says Hølaas.
From there, the carbon will be transported to a receiving terminal, and from there by pipeline into the North Sea and then pumped into porous rocks at a depth of over 2,500 metres. Denser rocks above the reservoir ensure that the gas does not leak out and end up in the atmosphere.
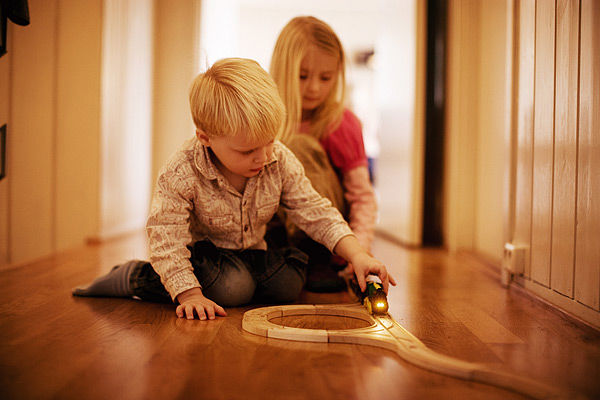
"Assuming positive results from the concept study, we will continue the CCS project until the final investment decision in the summer of 2027."
More about district heating
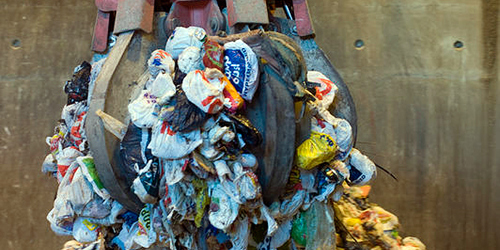
Mythbusting: "Burning waste to produce district heating is not climate-friendly"
Surplus heat from waste incineration is the largest energy source for district heating in Norway. So this cannot be particularly climate-friendly, or can it?
Read more
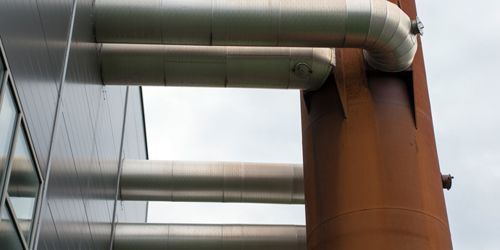
District heating: Urban energy
Warming up cities with resources that would otherwise be wasted is an important contribution towards a climate-neutral energy supply.
Read more